Unlocking the Secrets of Fused Deposition Modeling: Transform Your Ideas into Reality!
Fused deposition modeling (FDM) is a revolutionary 3D printing technology that has gained significant traction in recent years, becoming a cornerstone in various industries. Its ability to convert digital designs into tangible objects has opened up a world of possibilities for designers, engineers, and creators alike. The significance of FDM lies not only in its technical capabilities but also in its accessibility; many businesses and individuals are now turning to fused deposition modeling services to bring their innovative ideas to life. Whether it's for prototyping, production, or educational purposes, FDM services are transforming the landscape of manufacturing and design, making it easier than ever to turn concepts into physical products.
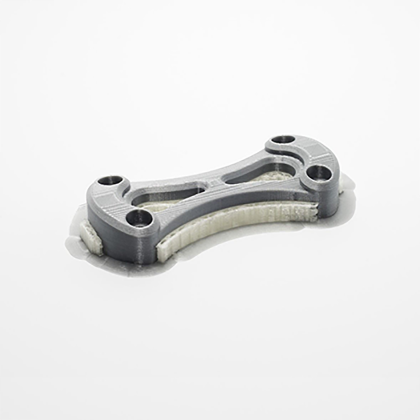
Understanding Fused Deposition Modeling Services
Fused deposition modeling services involve the use of specialized 3D printers that construct objects layer by layer, using thermoplastic materials. The technology relies on a process where a filament is heated until it melts and is then extruded through a nozzle onto a build platform, where it cools and solidifies. This layer-by-layer construction allows for intricate designs and complex geometries that would be difficult or impossible to achieve with traditional manufacturing methods. FDM services can cater to a wide range of customer needs, from creating prototypes for testing and validation to producing end-use parts for various applications. The materials used in FDM, which include plastics like ABS and PLA, can be selected based on the specific requirements of the project, enhancing the versatility of these services.
How Fused Deposition Modeling Works
The process of fused deposition modeling begins with the creation of a digital design using computer-aided design (CAD) software. This design is then sliced into individual layers by slicing software, which translates the 3D model into a format that the printer can understand. Once the printing process begins, the printer follows the instructions provided by the sliced file, depositing the melted filament layer by layer until the object is complete. Each layer bonds to the one below it, gradually building the final piece. After printing, post-processing may be required, including removal of support structures, sanding, or painting for a polished finish. Precision is crucial throughout this process; any misalignment or error can affect the integrity of the final product. Advanced technological features, such as automatic bed leveling and multi-material printing, further enhance the overall quality and accuracy of FDM prints.
Applications and Use Cases of FDM Services
Fused deposition modeling services are utilized across a diverse array of industries, showcasing their flexibility and effectiveness. In the automotive sector, FDM is used to create prototypes of parts, allowing engineers to test designs before mass production. The aerospace industry benefits from FDM's ability to produce lightweight components that meet stringent regulatory standards while maintaining structural integrity. In healthcare, FDM is making strides in creating custom prosthetics and dental devices tailored to individual patients. The education sector also leverages FDM services for hands-on learning experiences; students can engage in design and engineering projects, bringing their academic knowledge to life through 3D printing. Innovative projects abound, from creating intricate models of historical artifacts to developing functional tools that solve real-world problems. For instance, a friend of mine once used FDM to design and print a custom housing for a drone, significantly improving its performance and aesthetics.
Advantages of Choosing Fused Deposition Modeling Services
Choosing fused deposition modeling services comes with numerous advantages that make it an appealing option for many applications. Firstly, FDM is often more cost-effective than other 3D printing technologies, making it accessible for startups and small businesses. The versatility of materials used in FDM allows for a wide range of applications, with the option to choose from various thermoplastics suited to different project needs. Additionally, FDM is well-known for its rapid prototyping capabilities; designs can be turned into physical objects in a matter of hours, facilitating quick iterations and testing. Compared to other 3D printing methods, such as stereolithography (SLA) or selective laser sintering (SLS), FDM has a lower barrier to entry, as the equipment and materials are generally more affordable and easier to obtain. This makes FDM an attractive choice for individuals and companies looking to innovate without incurring exorbitant costs.
Embracing the Future of FDM Services
In conclusion, fused deposition modeling services represent a transformative force in the realm of 3D printing, significantly impacting various industries and applications. By understanding the intricacies of FDM, its working process, and the wide-ranging benefits it offers, individuals and businesses can harness its power to bring their ideas to life. As technology continues to evolve, the potential for FDM services is boundless, paving the way for even more innovative projects in the future. Whether you are an entrepreneur, an educator, or a hobbyist, considering fused deposition modeling for your next project could very well lead to exciting new possibilities.