Unlock the Secrets of Nylon Filament: Discover Its Game-Changing Benefits for 3D Printing!
Nylon filament has rapidly gained traction as a favored material in the 3D printing community, and for good reason. As enthusiasts and professionals alike explore the endless possibilities of additive manufacturing, understanding the properties and benefits of nylon filament becomes crucial for achieving optimal results. Its unique characteristics not only enhance the quality of prints but also expand their applicability in various fields. From intricate prototypes to functional components, nylon filament is transforming the landscape of 3D printing. This article delves into the essential aspects of nylon filament, shedding light on why it deserves a spot in your next printing project.
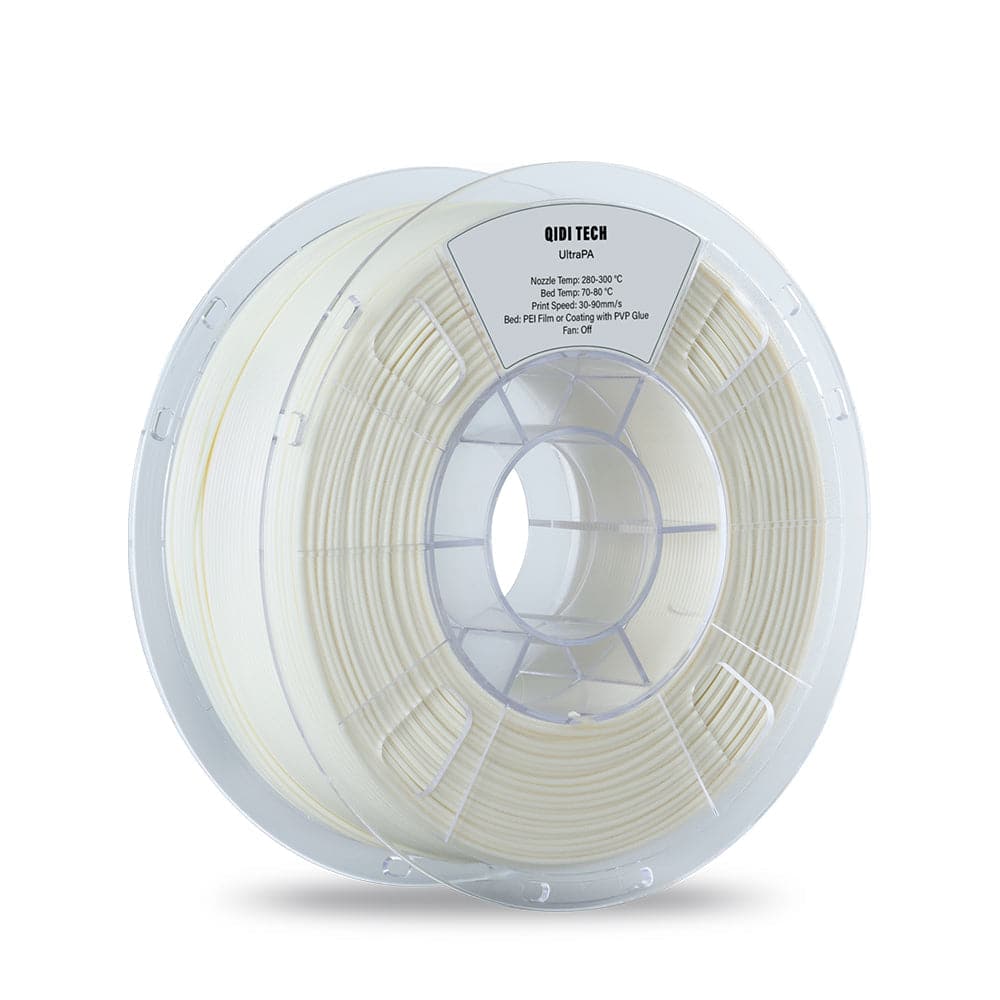
Understanding Nylon Filament
Nylon filament is a synthetic polymer that has become a staple in the world of 3D printing. Its composition primarily includes polyamide, which is known for its excellent mechanical properties and versatility. There are various types of nylon used in 3D printing, including Nylon 6, Nylon 66, and Nylon 12, each offering distinct characteristics suited for different applications. Nylon 6 is particularly popular for its ease of processing and good strength, while Nylon 66 boasts superior durability. Nylon 12, on the other hand, is often favored for its low moisture absorption, making it ideal for parts that require dimensional stability. Understanding these different types helps users choose the right filament for their specific needs, whether for prototyping or production.
Properties of Nylon Filament
One of the most appealing aspects of nylon filament is its incredible properties. It boasts a high strength-to-weight ratio, meaning it can withstand significant stress without adding unnecessary bulk to a project. This is particularly beneficial for applications requiring lightweight yet durable parts. Additionally, nylon filament offers excellent flexibility, allowing for the creation of intricate designs that can endure bending and twisting without breaking. However, one must also consider its moisture absorption properties; nylon can absorb water from the environment, which may affect its mechanical performance and print quality. It’s crucial for users to keep nylon filament dry and store it in a controlled environment to preserve its optimal performance. These properties significantly influence both the printing process and the final product, making it essential to harness them effectively.
Benefits of Using Nylon Filament in 3D Printing
Nylon filament presents numerous advantages over other common 3D printing materials such as PLA or ABS. Its superior strength-to-weight ratio allows for the creation of robust parts that do not compromise on weight, making it ideal for applications in automotive or aerospace industries. Furthermore, nylon's versatility means it can be used for both functional prototypes and end-use products, accommodating a wide array of designs. A friend of mine, who frequently works with 3D printing for automotive prototypes, shared how nylon filament enabled him to create lightweight yet durable components that performed exceptionally under stress tests. Additionally, nylon filament's ability to adhere well to itself during printing results in smoother finishes and fewer layer lines, which is a boon for aesthetic quality. These benefits make nylon filament a top choice for those looking to push the boundaries of 3D printing.
Applications of Nylon Filament in 3D Printing
The applications of nylon filament in 3D printing are vast and varied. In industries such as automotive and aerospace, it is commonly used for prototyping parts that require both durability and flexibility. Additionally, nylon’s resistance to wear and tear makes it suitable for producing functional components like gears, brackets, and fixtures. In the medical field, nylon filament is utilized for creating custom prosthetics and implants due to its biocompatibility and strength. Moreover, the fashion industry has also started to embrace nylon filament for creating intricate designs and accessories. For instance, a friend who creates custom 3D-printed jewelry found that nylon offered her the flexibility and durability she needed to craft unique pieces that could withstand daily wear. As industries continue to evolve, the applications of nylon filament are likely to expand, making it a material worth considering for innovative projects.
Summary of Key Insights on Nylon Filament
In summary, nylon filament stands out as a transformative material in the realm of 3D printing. Its remarkable properties, including strength, flexibility, and versatility, make it an invaluable asset for various applications across different industries. By understanding its composition and benefits, users can leverage nylon filament to create high-quality prototypes and end-use products. As you embark on your next 3D printing project, consider the game-changing potential of nylon filament to elevate your creations and expand your possibilities.