Unlocking the Magic of Nylon: Transform Your 3D Printing Experience!
Nylon filament has rapidly gained popularity in the 3D printing community, and for good reason. Its remarkable versatility and superior performance make it a go-to material for both hobbyists and professionals alike. With its unique properties, nylon allows for the creation of durable, flexible, and high-quality prints that stand the test of time. Imagine crafting intricate designs that not only look great but also hold up under pressure! As we dive deeper into the world of nylon filament, we will explore its key properties, the various types available, and the exciting applications that showcase its potential. Whether you're a seasoned printer or just starting, understanding nylon filament can open up new avenues for your 3D printing projects.
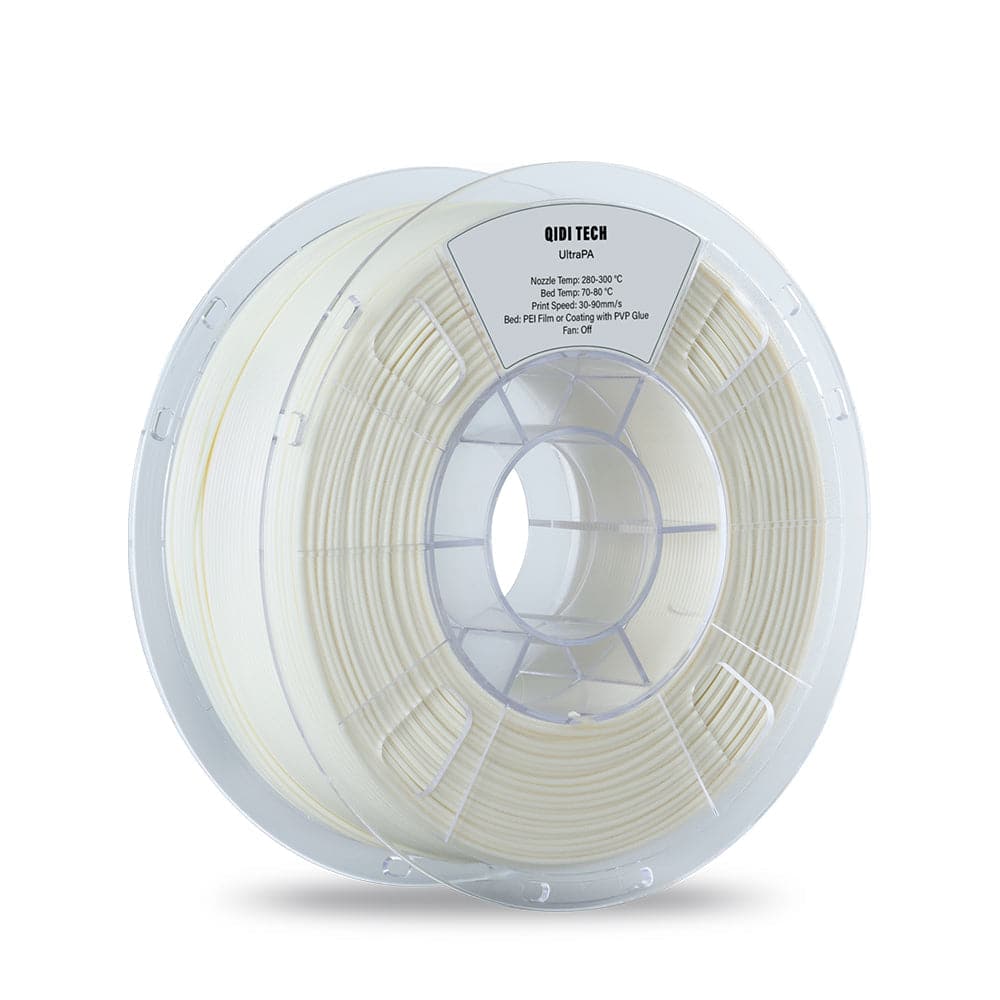
Understanding the Properties of Nylon Filament
The exceptional properties of nylon filament set it apart from other materials used in 3D printing. One of its most notable characteristics is its strength; nylon exhibits a tensile strength that rivals that of metals, making it ideal for functional parts that require durability. In addition to strength, nylon is also remarkably flexible, allowing it to bend and stretch without breaking, a feature that is particularly beneficial for creating complex geometries or parts that need to withstand repeated stress. Another critical property of nylon is its resistance to wear and chemicals. This makes nylon filament perfect for applications in harsh environments where parts are exposed to friction, heat, or corrosive substances. These properties combined contribute to nylon's performance in 3D printing, making it a reliable choice for creating parts that demand both resilience and versatility. A friend of mine who works in engineering recently used nylon for a prototyping project, and he was impressed by how well it held up under stress tests compared to other materials he had used in the past.
Types of Nylon Filament Available for 3D Printing
When it comes to nylon filament, there are several types to choose from, each with its own unique characteristics and benefits. One of the most common types is Nylon 6, known for its excellent strength and impact resistance. It is easy to print and offers good flexibility, making it suitable for a wide range of applications from functional prototypes to end-use parts. Another popular variant is Nylon 12, which boasts lower moisture absorption and better dimensional stability compared to Nylon 6. This makes it ideal for applications that require precise tolerances and durability in variable conditions. Additionally, there are specialty nylon filaments available that have been modified for specific applications. For instance, carbon fiber-infused nylon offers enhanced rigidity and strength, making it perfect for parts that need to endure high stress. With such variety, it’s crucial to select the right type of nylon filament based on the specific requirements of your project.
Applications of Nylon Filament in 3D Printing
Nylon filament has found its way into numerous industries, showcasing its versatility and effectiveness. In the automotive sector, it is often used to create lightweight, durable components that can withstand high temperatures and mechanical stress. For instance, many automotive manufacturers use nylon for parts like clips, brackets, and even functional prototypes to test designs before full-scale production. The aerospace industry also benefits from nylon’s properties, utilizing it for lightweight structural components and interior parts that require both strength and flexibility. Moreover, in the consumer products sector, nylon is frequently used to create custom tools, ergonomic handles, and even fashion accessories, demonstrating its wide-ranging applications. A friend of mine once printed a custom ergonomic grip for her camera using nylon filament, and she was thrilled with how well it fit her hand and enhanced her photography experience. The practicality and performance of nylon filament in real-world applications make it a valuable choice for various industries.
Tips for Working with Nylon Filament
Successfully printing with nylon filament does come with its own set of challenges, but with the right tips and techniques, you can achieve excellent results. Firstly, it’s essential to optimize your printing settings; a higher extrusion temperature typically works best for nylon, often around 240-260°C, depending on the specific type. Bed adhesion can also be tricky, as nylon tends to warp during cooling. Using a heated bed set to about 70-80°C, combined with a good adhesive such as a glue stick or specialized adhesive sprays, can significantly improve adhesion and reduce warping. Additionally, post-processing nylon prints can enhance their appearance and durability. Techniques such as sanding or dyeing can be employed to achieve a smooth finish or custom color. By keeping these tips in mind, you can unlock the full potential of nylon filament in your 3D printing projects.
Summary of Nylon Filament's Impact on 3D Printing
In summary, nylon filament stands out as a remarkable material in the 3D printing landscape, thanks to its impressive properties, diverse types, and wide-ranging applications. Its strength, flexibility, and resistance to wear make it an ideal choice for a variety of projects, from functional prototypes to end-use parts. Whether you're creating automotive components, aerospace structures, or unique consumer products, nylon filament can elevate your work to new heights. As you explore the possibilities of this versatile material, I encourage you to experiment with different types of nylon filament and techniques to discover what works best for your specific needs. The world of 3D printing is continually evolving, and nylon is at the forefront of this exciting innovation.