Unlock the Secrets of ABS Filament: Transform Your 3D Printing Game Today!
In the vibrant world of 3D printing, ABS filament stands out as a favorite among makers, hobbyists, and professionals alike. Known for its robust characteristics and versatility, ABS (Acrylonitrile Butadiene Styrene) has become a go-to material for a wide range of applications. Its popularity can be attributed to its excellent mechanical properties and the ease with which it can be printed, making it suitable for both beginners and seasoned experts in the field. This article will dive into the essential properties of ABS filament, explore its various uses in different industries, and provide best practices to ensure successful 3D printing experiences.
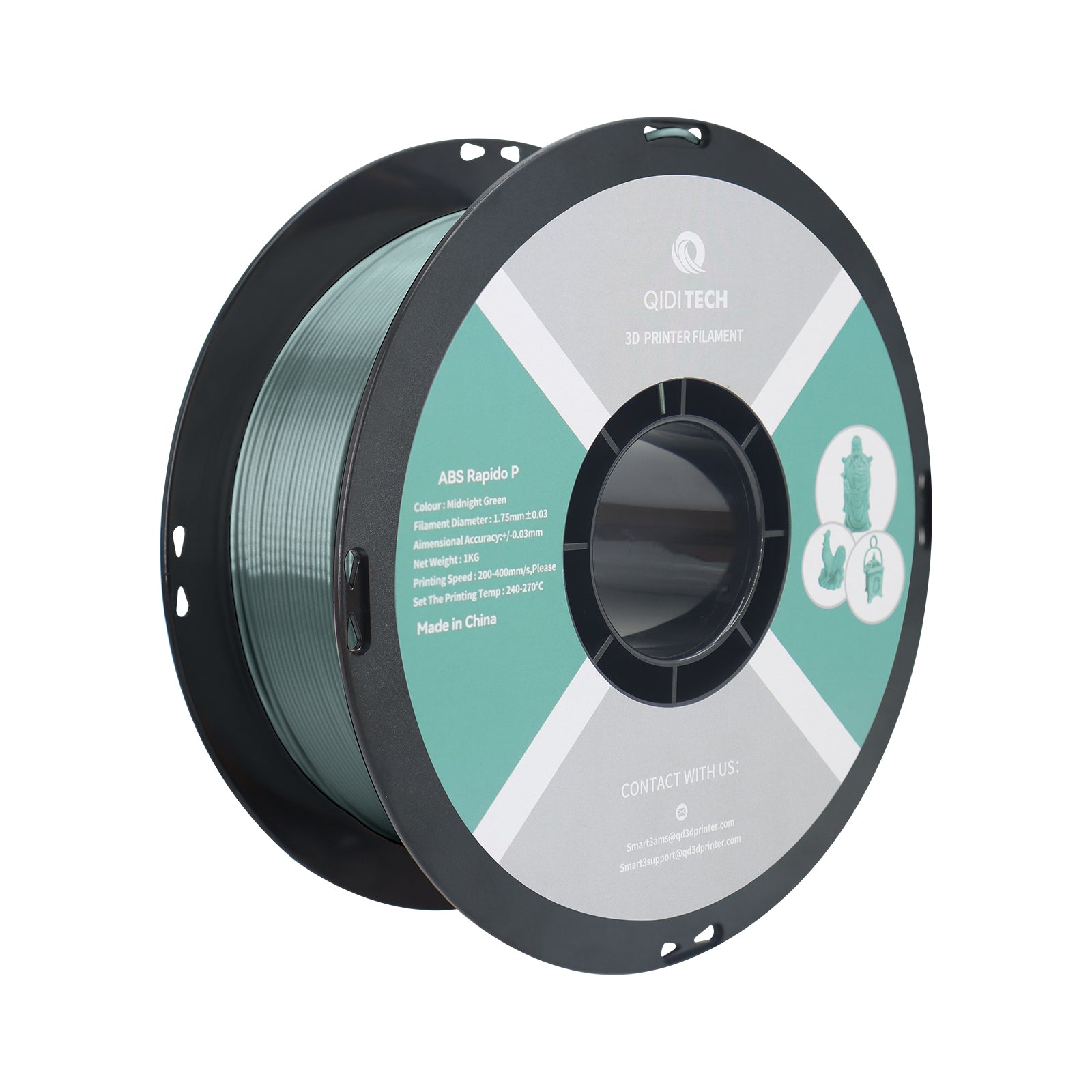
Understanding ABS Filament Properties
ABS filament is a thermoplastic polymer known for its impressive strength and resilience. Chemically, it is composed of three monomers: acrylonitrile, butadiene, and styrene, which contribute to its unique properties. The acrylonitrile component offers chemical resistance and thermal stability, while butadiene enhances toughness and impact resistance. Styrene adds rigidity and gloss, resulting in a filament that strikes a balance between flexibility and durability. One of the standout features of ABS filament is its ability to withstand higher temperatures compared to other materials like PLA, making it ideal for functional parts that may be exposed to heat. Additionally, ABS is relatively easy to post-process, allowing for sanding, painting, and gluing, which further expands its usability in various projects. For instance, a friend of mine recently used ABS to create a custom enclosure for his electronics project, and the heat resistance proved invaluable in ensuring the components were safe and functional.
Common Uses of ABS Filament in 3D Printing
ABS filament is widely used across multiple sectors due to its versatility and reliable performance. In prototyping, designers and engineers often choose ABS for creating functional prototypes that can be tested thoroughly before moving to mass production. This material's durability and ability to mimic the properties of final products make it an ideal choice for preliminary testing. In the manufacturing sector, ABS is frequently employed to produce parts for various applications, such as automotive components, household items, and even toys. The advantages of using ABS in these settings include its strength, lightweight nature, and resistance to impact, which contribute to the longevity and effectiveness of the products. Additionally, industries such as robotics and aerospace leverage ABS filament for creating custom parts that require precision and resilience. A colleague of mine, who works in the automotive industry, once shared how ABS was crucial in developing a prototype for a new car part that needed extensive testing for durability under varying conditions.
Best Practices for 3D Printing with ABS Filament
To achieve the best results when printing with ABS filament, it is essential to follow some best practices that can significantly enhance the quality of your prints. First and foremost, ensuring proper printer settings is crucial. A heated bed is a must when working with ABS, as it helps prevent warping during the cooling process. Setting the bed temperature between 90°C and 110°C is generally recommended, while the nozzle temperature should be around 220°C to 250°C, depending on your specific printer. Another important aspect is bed adhesion; using a glue stick or a specialized adhesion spray can help keep the print in place as it builds. Additionally, controlling the ambient temperature is vital since ABS can warp if it cools too quickly. Many experienced users recommend enclosing the printer to maintain a stable temperature environment. After printing, post-processing techniques like sanding and acetone vapor smoothing can be employed to achieve a polished finish, enhancing the aesthetics of the final product. A friend of mine, who regularly prints with ABS, swears by using an enclosure to maintain temperature stability, and he has seen a significant reduction in warping issues since implementing this practice.
Final Insights on ABS Filament
In summary, understanding the properties, uses, and best practices associated with ABS filament is essential for anyone looking to improve their 3D printing results. Its strength, heat resistance, and versatility make it a favored material across various applications, while proper knowledge of printer settings and post-processing techniques can greatly enhance print quality. As you embark on your 3D printing journey, don't hesitate to experiment with ABS filament in your projects. With a bit of practice and the right approaches, you'll unlock the full potential of this remarkable material and take your 3D printing skills to new heights.