Unlocking the Secrets of FDM 3D Printing: Discover Its Power and Potential!
In the realm of modern manufacturing, FDM 3D printing technology has emerged as a transformative force, capturing the interest of engineers, designers, and hobbyists alike. Fused Deposition Modeling (FDM) allows for the creation of intricate designs that were once limited by traditional manufacturing techniques. This growing interest stems from the technology's accessibility, versatility, and the potential it holds for innovation. In this article, we will delve into the fundamentals of FDM 3D printing, unravel how it works, explore its advantages and disadvantages, and examine the myriad of applications that are shaping industries today. Whether you are a curious beginner or a seasoned professional, understanding FDM technology can open new avenues for creativity and efficiency.
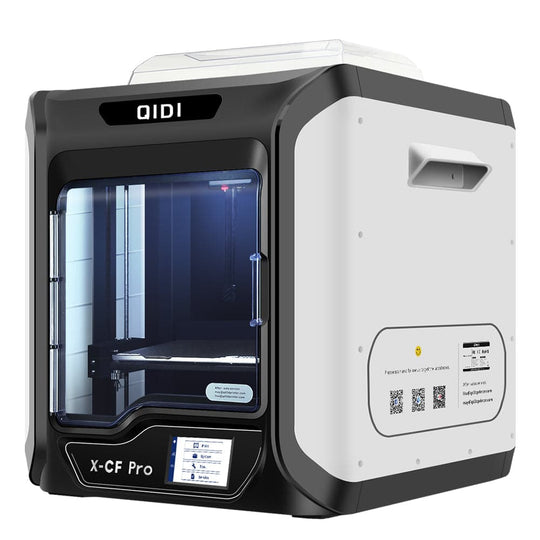
Understanding FDM 3D Printing Technology
Fused Deposition Modeling (FDM) is a 3D printing technology that constructs objects layer by layer through the extrusion of thermoplastic materials. The concept was first introduced by Scott Crump in the late 1980s, who later co-founded a company that became a leader in the 3D printing industry. FDM fits within the broad category of additive manufacturing, where materials are added layer by layer to create a final product, as opposed to subtractive manufacturing, which involves cutting away material from a larger block. FDM has gained popularity due to its user-friendly nature, making it suitable for both professional and personal projects. The ability to create complex geometries with minimal waste has positioned FDM as a go-to technology for prototyping and production across various sectors.
How FDM 3D Printing Works
The FDM printing process begins with a 3D model, typically created using computer-aided design (CAD) software. Once the model is ready, it is sliced using specialized software that prepares it for printing by breaking it down into thin horizontal layers. The printer then heats a thermoplastic filament, which is fed through an extruder. This extruder moves along the X and Y axes, depositing melted filament onto a heated build platform layer by layer. As each layer is applied, it cools and solidifies, bonding to the layer beneath it. The printer continues this process until the entire object is built. Key components of an FDM printer include the extruder, which controls the flow of filament, and the build platform, which provides a stable surface for the printed object. Understanding these components and their functions is essential for troubleshooting and optimizing print quality.
Advantages of FDM 3D Printing
One of the most significant advantages of FDM technology is its cost-effectiveness. Compared to other 3D printing methods, FDM printers and materials are generally more affordable, making it accessible for hobbyists and small businesses. Additionally, FDM supports a wide variety of thermoplastic materials, including PLA, ABS, and PETG, each offering different properties suitable for various applications. The simplicity of the operation is another benefit; users can easily learn to operate an FDM printer, often with minimal training. This has led to a surge in the technology's use in educational settings, where students can explore engineering and design concepts hands-on. Moreover, the capability to produce functional prototypes quickly and iteratively makes FDM a favored choice for professionals looking to streamline their design processes.
Disadvantages of FDM 3D Printing
Despite its many advantages, FDM 3D printing does come with limitations. One common issue is print quality, especially in complex designs where overhangs and intricate details may not come out as intended. Layer adhesion can also be inconsistent, affecting the strength and durability of the final product. Print speed is another drawback; while FDM can produce objects relatively quickly, larger items may take several hours or even days to complete. Additionally, the materials used in FDM printing can be limited in terms of mechanical properties, such as heat resistance and flexibility, making them unsuitable for certain applications. Users must carefully consider these factors when choosing FDM for their projects.
Potential Applications of FDM 3D Printing
The versatility of FDM technology has led to its adoption in various fields. In prototyping, engineers can quickly create and test designs, significantly reducing development time. In education, FDM printers are being used to teach students about engineering and design principles, allowing them to bring their ideas to life. The healthcare industry has also seen innovative applications, such as creating custom prosthetics and surgical models tailored to individual patients' needs. Furthermore, FDM is making waves in manufacturing, where small-scale production runs and customized products can be produced efficiently. For instance, a friend of mine recently started a small business creating custom phone cases using an FDM printer, showcasing the technology's potential for entrepreneurship. The possibilities are endless, and as FDM continues to evolve, its impact on various sectors will only grow.
Maximizing the Potential of FDM 3D Printing
In summary, FDM 3D printing technology presents a remarkable opportunity for innovation across multiple industries. Understanding how this technology works, along with its advantages and disadvantages, is crucial for anyone looking to leverage its potential. From prototyping to education and manufacturing, FDM is transforming traditional processes and enabling creativity like never before. As you explore the world of 3D printing, consider how FDM technology can enhance your projects and inspire new ideas. The journey into additive manufacturing is just beginning, and the possibilities are limited only by our imagination.