Unlock the Secrets of Nylon Filament: Revolutionize Your 3D Printing Experience!
Nylon filament has emerged as a game-changer in the world of 3D printing, rapidly gaining popularity among both hobbyists and professionals. Known for its exceptional properties, nylon offers a unique blend of strength and flexibility that sets it apart from other materials. As the 3D printing industry continues to evolve, understanding the characteristics and benefits of nylon filament becomes essential for anyone looking to enhance their printing capabilities. Whether you're a seasoned expert or just starting your printing journey, diving into the world of nylon filament can unlock new possibilities and improve your overall printing experience.
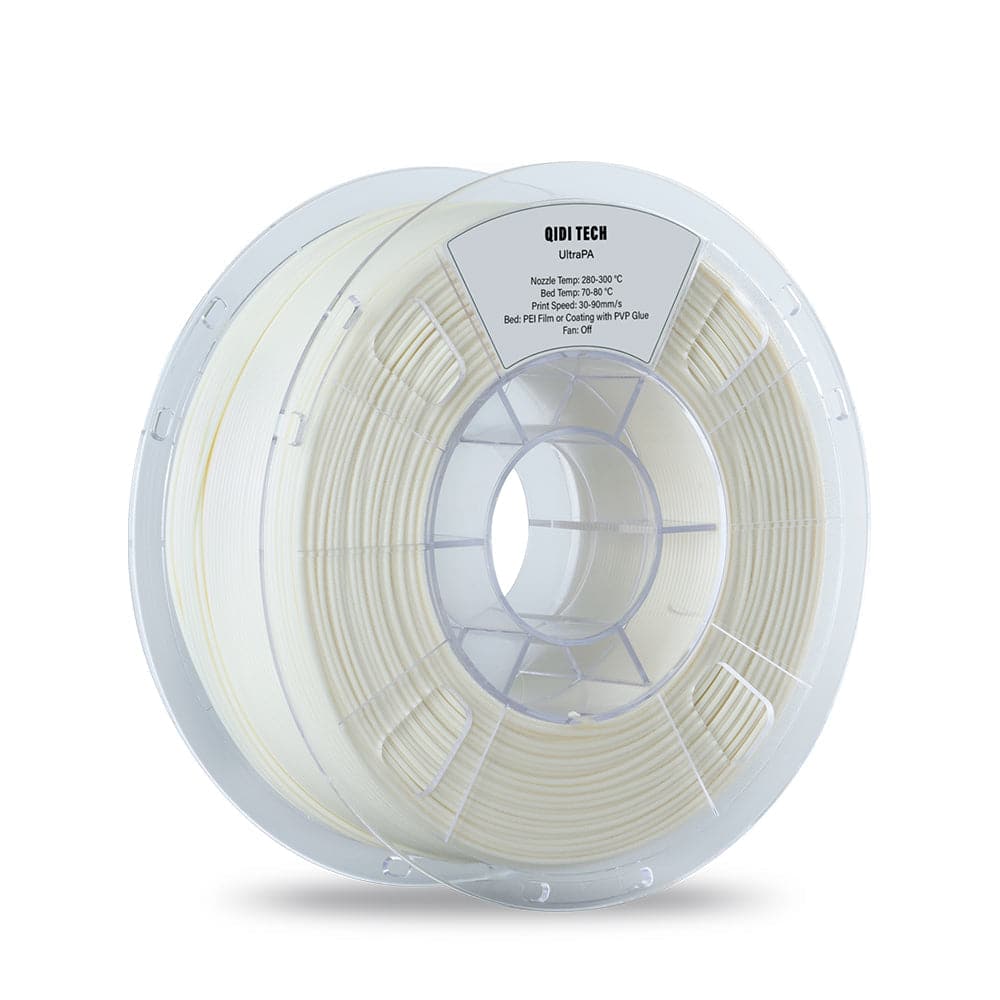
Understanding Nylon Filament
Nylon filament is a synthetic polymer made from polyamide, which is known for its remarkable chemical and physical properties. Comprising long chains of repeating units, this filament is produced through a process called polymerization, where monomers are chemically bonded together. One of the most notable characteristics of nylon is its ability to absorb moisture, which can affect its printing properties if not managed properly. There are several types of nylon filaments available, including nylon 6, nylon 12, and nylon 645, each varying in their strength, flexibility, and printability. For instance, nylon 6 is often recognized for its toughness and resistance to impact, while nylon 12 offers better dimensional stability. Understanding these unique characteristics can help you select the right type of nylon filament for your specific 3D printing needs.
Benefits of Using Nylon Filament in 3D Printing
The benefits of using nylon filament in 3D printing are numerous, making it a preferred choice for many applications. One of the primary advantages is its exceptional strength-to-weight ratio, which allows for the creation of lightweight yet durable parts. This filament is not only strong but also incredibly flexible, enabling it to withstand bending and stretching without breaking. Nylon's resistance to wear and impact makes it ideal for functional prototypes and end-use parts that require longevity and reliability. Moreover, its lightweight nature contributes to reduced printing costs and efficient material usage, making it an economical choice for various projects. Personally, I had a friend who printed a series of mechanical parts for a robotics project using nylon filament, and the results were impressive—strong and functional parts that held up remarkably well under stress.
Applications of Nylon Filament
Nylon filament is utilized across various industries due to its versatile properties. In the automotive sector, it is commonly used to produce functional components like gears, brackets, and clips that require both durability and flexibility. The aerospace industry also benefits from nylon's lightweight characteristics, employing it for interior parts and prototypes that need to meet stringent weight and strength requirements. In fashion, designers are leveraging nylon filament to create intricate patterns and wearable technology, showcasing its potential in the realm of textiles. Additionally, the manufacturing industry employs nylon for producing tooling, fixtures, and custom parts that demand high-performance standards. The diverse applications of nylon filament demonstrate its adaptability and effectiveness in meeting the needs of different sectors.
Tips for Successful 3D Printing with Nylon Filament
Successfully printing with nylon filament requires some specific techniques to achieve optimal results. First, ensure that your printer is equipped with an all-metal hotend, as nylon typically requires higher temperatures to extrude properly. Additionally, optimal bed adhesion is crucial to prevent warping; using a heated bed set to around 70-80 degrees Celsius can help with this. Some users also recommend using a glue stick or a specialized adhesive to further improve bed adhesion. Post-processing methods, such as annealing, can also enhance the strength of printed parts. Taking these steps can significantly improve your experience when working with nylon filament, ensuring that your final prints meet your expectations.
Maximizing Your 3D Printing Potential with Nylon
In conclusion, nylon filament is a powerful material that can greatly enhance your 3D printing projects. With its unique properties, including strength, flexibility, and resistance to wear, nylon filament offers numerous advantages over other materials. Whether you're creating prototypes, functional parts, or artistic designs, understanding how to effectively use nylon can open up new avenues in your printing endeavors. As you experiment with nylon filament, you may discover its potential to revolutionize your 3D printing experience, making it a worthwhile addition to your material repertoire.