Unveiling the Battle of 3D Printing: FDM vs. SLA – Which Will Rule Your Projects?
In today's rapidly evolving world of technology, 3D printing has emerged as a revolutionary force in manufacturing and prototyping. Among the various techniques available, Fused Deposition Modeling (FDM) and Stereolithography (SLA) stand out as the most widely used methods. Each technology has its unique characteristics that cater to different needs, whether it’s for rapid prototyping, artistic endeavors, or functional parts production. Understanding these differences is crucial for anyone looking to harness the true potential of 3D printing. This article will delve into the workings of both FDM and SLA technologies, elucidating their advantages and disadvantages, and ultimately guiding you in selecting the most suitable method for your projects.
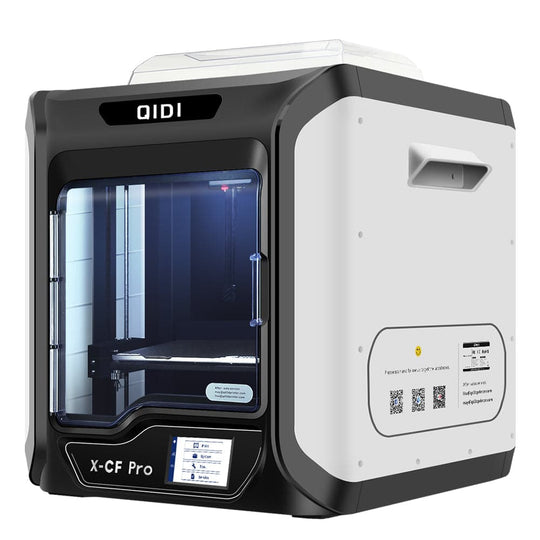
Understanding FDM 3D Printing
FDM technology operates by melting thermoplastic filament and extruding it layer by layer to create a 3D object. This process is akin to a hot glue gun, where the filament is heated to its melting point and deposited onto a build platform. The typical materials used in FDM include ABS, PLA, and PETG, each offering different properties that can impact the final product. FDM is renowned for its cost-effectiveness and user-friendly nature, making it an excellent choice for hobbyists and small businesses alike. One of the significant advantages of FDM is its accessibility; printers are widely available, and the materials are relatively inexpensive compared to those used in SLA. Moreover, the simplicity of the technology means that users can often troubleshoot issues without specialized knowledge.
However, FDM isn't without its challenges. The surface finish of FDM prints often leaves much to be desired, with visible layer lines and a rough texture that may not be suitable for all applications. Additionally, the speed of FDM printing can be a double-edged sword; while it can produce parts quickly, the layer-by-layer method can lead to longer print times for intricate designs. A friend of mine who dabbles in 3D printing for model making once expressed his frustration with the visible lines on his FDM prints, which were especially pronounced in his detailed miniatures. Despite these limitations, FDM remains a popular choice due to its versatility and ease of use.
Exploring SLA 3D Printing
SLA technology takes a different approach by utilizing a laser to cure liquid resin into solid form. The process begins with a resin vat, where a UV laser traces the desired pattern on the surface of the resin. The laser selectively cures the resin layer by layer, allowing for incredibly high levels of detail and smooth surface finishes. The resins used in SLA printing come in various formulations, including standard, flexible, and tough resins, each tailored for specific applications, from intricate jewelry designs to durable functional parts.
The advantages of SLA are clear: it produces stunningly high-resolution prints with excellent surface quality, making it ideal for applications that demand precision, such as dental models or intricate prototypes. However, these benefits come at a cost. SLA printers and their associated resins tend to be more expensive than FDM options, which can be a barrier for hobbyists or small businesses. Additionally, SLA printing typically requires more post-processing, such as washing and curing the prints, which can add time to the workflow. A colleague of mine who works in product design shared his experience with SLA printing; the level of detail achieved was unparalleled, but he often found himself spending extra hours cleaning and finishing the models.
Comparative Analysis: FDM vs. SLA
When comparing FDM and SLA, several key differences become apparent that can influence your choice of technology. Speed is one of the most significant factors; FDM printers generally have faster print speeds for larger parts, while SLA excels in producing high-quality prints with complex details, albeit at a slower pace. In terms of cost, FDM is the more economical choice, both in terms of initial investment and material costs, making it more accessible for beginners and those on a budget.
Material options also differ between the two technologies. FDM offers a wide array of thermoplastics, while SLA primarily relies on photopolymer resins, which can have specific properties that cater to niche applications. Finally, the quality of the final product is often where SLA shines, delivering smooth and detailed prints that FDM struggles to match. However, FDM's durability and functional capabilities make it suitable for practical applications where strength is necessary. Understanding these distinctions can help you determine which technology aligns best with your project requirements and goals.
Choosing Between FDM and SLA
In the battle of 3D printing technologies, both FDM and SLA present unique advantages and challenges that can significantly impact your projects. FDM offers cost-effectiveness and ease of use, making it a favored choice for many enthusiasts and businesses. On the other hand, SLA provides unparalleled detail and smooth finishes, ideal for high-precision applications, albeit with a higher cost and greater post-processing needs. Ultimately, the decision between FDM and SLA should be guided by your specific project requirements, budget, and desired outcomes. By weighing the pros and cons of each technology, you can make an informed choice that enhances your 3D printing experience and meets your creative aspirations.