Unlocking the Magic of Laser Sintering: Transforming 3D Printing as You Know It!
In the ever-evolving landscape of 3D printing, laser sintering service stands out as a transformative technology that enhances both creativity and functionality. At its core, laser sintering is a method of additive manufacturing that utilizes a powerful laser to fuse powdered materials into solid structures, layer by layer. This innovative process has garnered significant attention for its ability to create intricate designs and functional prototypes, making it an invaluable asset across various industries. As organizations increasingly seek efficient and customizable solutions, laser sintering is poised to revolutionize traditional manufacturing practices, offering a glimpse into a future where imagination knows no bounds.
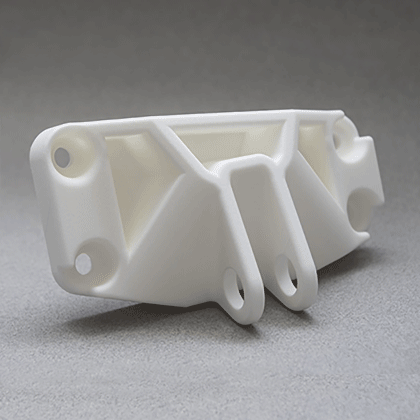
Understanding Laser Sintering
Laser sintering is a sophisticated additive manufacturing technique that employs a high-powered laser to selectively melt and fuse powdered materials, typically thermoplastics or metals, into a solid object. The process begins with a computer-aided design (CAD) model, which is sliced into thin layers. A thin layer of powder is spread across the build platform, and the laser scans the surface, melting the powder in the pattern dictated by the CAD file. Once the layer is complete, the platform lowers slightly, and a new layer of powder is applied, repeating the process until the object is fully formed. This layer-by-layer approach allows for complex geometries and designs that would be nearly impossible to achieve through traditional manufacturing methods. The significance of sintering lies in its ability to create parts with high precision and intricate details, making it a preferred choice in industries where complexity and performance are paramount.
Applications of Laser Sintering in 3D Printing
The applications of laser sintering are vast and varied, permeating fields such as aerospace, automotive, healthcare, and consumer products. In aerospace, for instance, companies leverage laser sintering to produce lightweight yet durable components that enhance fuel efficiency and performance. The ability to create intricate lattice structures contributes to weight reduction without compromising strength. In the automotive sector, laser sintering is used to develop prototypes and end-use parts with complex geometries, enabling faster design iterations and reduced time to market. Healthcare is another area where this technology shines; custom implants and prosthetics tailored to individual patients can be produced with high accuracy. Personal anecdotes from friends in the engineering field reveal how laser sintering has allowed them to experiment with innovative designs and create prototypes that were once mere ideas. Whether it's designing custom-fit dental devices or creating unique consumer products, laser sintering is reshaping the way we think about manufacturing.
Advantages of Laser Sintering Services
Utilizing laser sintering services comes with a plethora of advantages that set it apart from traditional manufacturing methods. One of the most significant benefits is design flexibility; designers can create intricate and complex geometries that are often impossible to fabricate using conventional techniques. The material efficiency of laser sintering is also noteworthy, as it generates minimal waste by using only the powder required for the final product. This aspect not only reduces costs but also aligns with the increasing demand for sustainable manufacturing practices. Furthermore, laser sintering enables the production of highly customized products tailored to individual specifications, thereby enhancing user satisfaction. The ability to produce parts in small batches without the need for extensive tooling translates to faster lead times and reduced overhead costs. As industries continue to embrace innovation, the advantages of laser sintering services make it an attractive solution for businesses looking to stay ahead of the competition.
Challenges and Limitations
Despite its many benefits, laser sintering is not without its challenges and limitations. One of the primary hurdles is the range of materials that can be effectively used in the process, as not all powders are suitable for sintering. Additionally, the costs associated with laser sintering equipment and materials can be prohibitive for smaller businesses. Speed of production is another concern, as the layer-by-layer method can be time-consuming, especially for larger parts. Ongoing research and development efforts are focused on addressing these challenges, with advancements in material science and technology promising to expand the capabilities of laser sintering. As more industries recognize the potential of this technology, overcoming these limitations will be crucial in fully unlocking its transformative power.
Revolutionizing Manufacturing with Laser Sintering
In summary, laser sintering represents a significant leap forward in the realm of 3D printing, offering innovative solutions that cater to the demands of various industries. Its ability to create complex geometries, coupled with the advantages of material efficiency and customization, positions laser sintering as a game-changer in manufacturing. While challenges remain, ongoing advancements in technology and materials promise a bright future for this field. As we look ahead, it's essential for businesses and individuals to consider the potential of laser sintering in their own applications, embracing the opportunities it presents to innovate and redefine traditional manufacturing paradigms.